
Innováció
Moduláris automatika a termelési hatékonyság jegyében
Multifunkciós szerelő- és mérősort fejlesztett a magyar gyártó
A modern ipari gyártásban egyre nagyobb szerepet kap a rugalmasság és az automatizálás, ám a két szempont gyakran ellentmondásba kerül. Egy magasan automatizált célgép ritkán rugalmas, egy általánosabb eszköz pedig nehezebben automatizálható. Az összetett elvárást jól mutatja az angol „mass customization” kifejezés, melynek a gyártóberendezéseket fejlesztő cégek mind inkább moduláris, nagy szabadságot kínáló gépekkel, cellákkal igyekeznek megfelelni. Az eddig Siemens, Fanuc és KUKA által fémjelzett jövőhöz most egy igencsak versenyképes magyar innováció zárkózott fel, amikor az Amplio Automatika bemutatta Modular Flexible Assembly Station nevű fejlesztését.
A vállalatok versenyképessége múlik azon, hogy minél hatékonyabb termelési folyamatokat alkalmazzanak, ám a magasan automatizált célgépek jellemzően csak nagyobb szériáknál gazdaságosak; a piaci kereslet ingadozása komoly problémát jelenthet a hagyományos, merev gyártósorok számára. Átalakításuk idő- és forrásigényes, ami rontja a gyártók alkalmazkodóképességét. Egy 2023-as[1] tanulmány szerint a rugalmas gyártási rendszerek bevezetése akár 50%-kal csökkentheti az átállási időt, amikor egy cég új termékek gyártására vált.
A választ a moduláris rendszerek jelentik, melyek az ipar 4.0 követelményeinek megfelelően biztosítják a kisszériás gyártás magas fokú flexibilitását, és tapasztalatok szerint akár 30-40%-kal növelhetik a termelékenységet a hagyományos rendszerekhez képest. Ennek eredői a kevesebb állásidő, a nagyobb termelékenység és a költségcsökkentés. A fentiek miatt nem meglepő, hogy a moduláris gyártási rendszerek az utóbbi években egyre népszerűbbé váltak, különösen az autóiparban, az elektronikai iparban és az orvostechnikai eszközök gyártásában. A McKinsey 2019-es tanulmánya[2] szerint a moduláris gyártás piaca évente 7-10%-os növekedést mutat, és 2030-ra várhatóan eléri a 150 milliárd dolláros értéket.
Egy másik meghatározó trend a mesterséges intelligencia és az IoT (Internet of Things) integrációja a moduláris gyártásba. Egy friss kutatás szerint[3] a mesterséges intelligenciával támogatott moduláris rendszerek önmagukban is akár 20%-kal csökkentik az állásidőt és 25%-kal növelik a gépek kihasználtságát. Egy 2023-as piaci jelentés[4] szerint az adaptív automatizálás megoldásai 2030-ra várhatóan a gyártási folyamatok 70%-ában jelen lesznek ‒ a mai számokat látva ez robbanásszerű keresletnövekedést jelent és óriási növekedési potenciált az olyan innovatív vállalatok számára, mint az Amplio Automatika.
A moduláris rendszerek használata egyébiránt jól korrelál az adott ország általános versenyképességével is, ahogy azt az ábra is mutatja. Emiatt egyfelől tekinthetünk erre a technológiára indikátorként, másfelől bizonyos ok-okozati összefüggés is vélelmezhető. Mindezek alapján kijelenthető, hogy az Amplio Automatika fejlesztése nemcsak jól időzített, de a legerősebb trendeket egyesíti egy olyan új eszközben, ami sok tekintetben nemcsak eléri, de felül is múlja a jelenleg piacon lévő megoldásokat.
Az Amplio Automatika Modular Flexible Assembly Station nevű rugalmas összeszerelő- és tesztelőcellája kialakítástól függően akár 10-12 állomáson is működhet párhuzamosan, az egyes állomások pedig szabadon variálhatók, gyorsan átszervezhetők az aktuális gyártási elvárások szerint. A manipulációs fázisok választéka nagyon széles. Összeszerelés, ragasztás, hegesztés, paszta adagolása, csavarozás, préselés, elektromos funkciótesztek, végtesztelés, számtalan féle mérés, akár programozás is, mindez egyetlen gépen belül. Több gépet összekapcsolva komplett sorokat is ki lehet alakítani. A rugalmasságot a beállítófelület is növeli, mivel grafikus megoldása nem igényel programozási ismereteket. A gép további előnye, hogy forgóasztalos építése miatt nagyon kompakt a megszokott berendezésekhez képest, miközben sem tartósságban, sem funkcióban nem kíván kompromisszumokat, termelési kapacitása és várható élettartama összemérhető a legnagyobb gyártókéval, miközben TCO tekintetében jellemzően megelőzi azokat. A cella méretei rugalmasak, tervezhető alapterületűek. Az ipar 4.0 egyik alappillére az intelligens és adaptív rendszerek fejlesztése, amelyek képesek alkalmazkodni a folyamatosan változó feltételekhez. Az olyan, jelen fejlesztésben is megtalálható technológiák, mint az önkonfiguráció (self-configuring systems) és a gépi tanulással támogatott optikai vizsgálatok lehetővé teszik, hogy a gyártási rendszerek valós időben reagáljanak az eltérésekre, minimalizálva az emberi beavatkozás szükségét.
Az állomások moduláris felépítése révén az összeszerelési folyamatok gyorsan és hatékonyan adaptálhatók az aktuális gyártási követelményekhez. A fejlesztés során a méret és a hatékonyság mellett nagy figyelmet fordítottak a munkaállomások ergonómiájára is. Az operátorok könnyedén hozzáférhetnek a szükséges eszközökhöz, a munkakörnyezet pedig végig biztonságos és kényelmes marad. Az Amplio Automatika innovációja ezzel hozzájárul az ipar 4.0 szélesebb körű alkalmazásához, és lehetővé teszi a vállalatok számára, hogy gyorsan és hatékonyan reagáljanak a piaci változásokra, biztosítva ezzel fenntartható növekedésüket az ipari automatizálás területén. A most létrehozott és már sorozatban gyártott, rendelhető Modular Flexible Assembly Station nem végállomása egy folyamatnak, hanem az első mérföldköve, mert a vállalat tovább bővíti kutatás-fejlesztési kapacitásait az intelligens robotika és az adaptív automatizálás terén.
[1] https://www.researchgate.net/publication/376260586_Flexible_Manufacturing_Systems_Performance_Analysis_and_Improvement
[2] https://www.mckinsey.com/capabilities/mckinsey-digital/our-insights/five-fifty-fast-and-modular
[3] https://www.researchgate.net/publication/386602312_AI-Based_Predictive_Maintenance_for_US_Manufacturing_Reducing_Downtime_and_Increasing_Productivity
[4] https://www.grandviewresearch.com/industry-analysis/manufacturing-automation-market-report
Modular Automation – Hungarian Manufacturer Develops a Multifunctional Assembly and Measurement Line
An automated dedicated machine is rarely flexible, while a more general-purpose device is harder to automate. To meet these complex requirements, companies developing manufacturing equipment strive to create modular machines and cells. Until now, the future of automation has been defined by Siemens, Fanuc, and KUKA, but a Hungarian innovation has now joined the ranks. Amplio Automatika has introduced its latest development, the Modular Flexible Assembly Station.
In recent years, modular systems have gained increasing popularity, particularly in the automotive, electronics, and medical device industries. According to a 2019 McKinsey study[5], the market for such equipment has been growing at an annual rate of 7-10% and is expected to reach a value of $150 billion by 2030. A 2023 market report[6] predicts that adaptive automation solutions will be present in 70% of manufacturing processes by 2030. Given today’s figures, this suggests an explosive rise in demand and immense growth potential for innovative companies like Amplio Automatika.
The Modular Flexible Assembly Station developed by Amplio Automatika can operate with up to 10-12 stations running in parallel. Each station is freely configurable and can be quickly restructured. The system supports a wide range of manipulation processes, including assembly, gluing, welding, pasting, screwing, pressing, cabling, electrical function tests, final testing, various types of measurements, and even programming—all within a single machine. By connecting multiple machines, complete production lines can be formed.
The graphical setup interface does not require programming knowledge, making it highly user-friendly. Another advantage of the machine is its rotary table design, which makes it exceptionally compact while maintaining production capacity and expected lifespan comparable to the largest manufacturers. In terms of total cost of ownership (TCO), it often outperforms competing solutions.
Cutting-edge technologies such as master data-based self-configuring systems and machine learning-assisted process optimization, both featured in this development, allow manufacturing systems to respond to deviations in real time, minimizing the need for human intervention. Throughout the development process, alongside size and efficiency considerations, significant attention was also given to ergonomics and workplace safety.
[5] https://www.mckinsey.com/capabilities/mckinsey-digital/our-insights/five-fifty-fast-and-modular
[6] https://www.researchgate.net/publication/386602312_AI-Based_Predictive_Maintenance_for_US_Manufacturing_Reducing_Downtime_and_Increasing_Productivity
További friss híreket talál az ipar4.hu főoldalán! Kövesse a technológiai híreket és csatlakozzon hozzánk a Facebookon is!
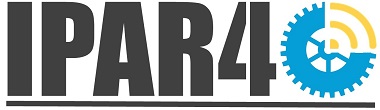